Precision Plastic Molding: Revolutionizing Manufacturing Processes
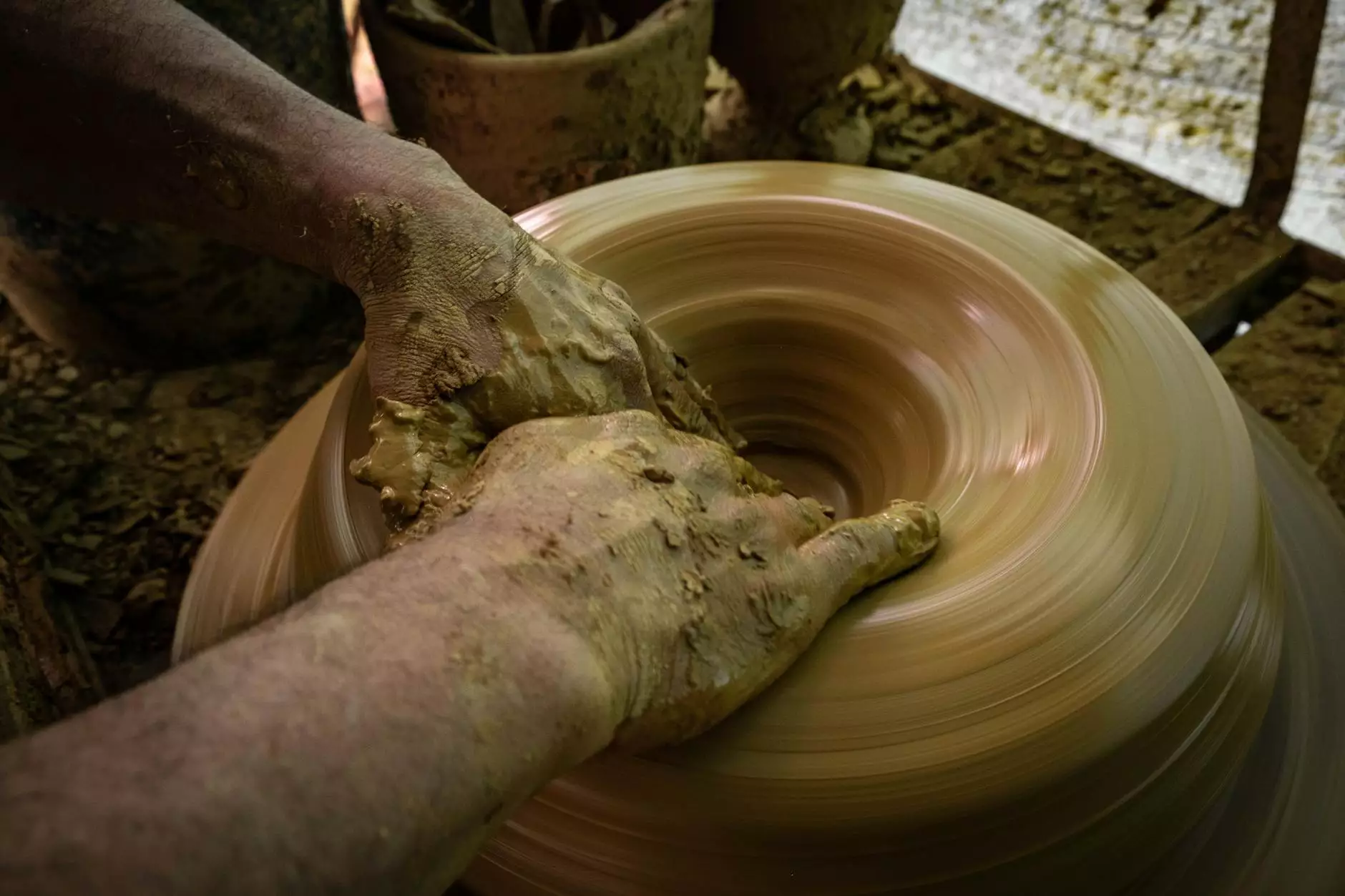
Understanding Precision Plastic Molding
Precision plastic molding is an advanced manufacturing technique that involves the creation of intricate plastic components with exceptional accuracy and detail. This innovative process has transformed industries by providing tailored solutions that meet the specific needs of various applications. With a focus on precision, manufacturers can achieve high-quality products that are not only functional but also visually appealing.
The Importance of Precision in Plastic Molding
In today's competitive market, precision has become a critical factor for success. As businesses strive to deliver superior products, the ability to produce components that adhere to strict specifications is paramount. Precision plastic molding offers several advantages:
- Consistent Quality: Components produced through precision molding are uniform and consistent in size, shape, and texture.
- Reduced Waste: This process minimizes material waste, as the exact amount of plastic is used to create each part.
- Enhanced Performance: Precise moldings ensure that components function as intended, resulting in improved product performance.
- Cost Effectiveness: By reducing errors and optimizing material use, businesses can achieve significant cost savings.
The Process of Precision Plastic Molding
The process of precision plastic molding involves several key steps that ensure the highest quality and accuracy in the final product:
- Design: The first step is creating a detailed design of the component using CAD software. This design includes specifications for dimensions and tolerances.
- Mold Fabrication: Skilled engineers fabricate molds based on the design. These molds are often made from high-grade steel or aluminum to withstand high pressure and heat during the molding process.
- Injection: Plastic pellets are heated until they melt and then injected into the mold. The precision of the injection process is vital to ensure that the molten plastic fills the mold completely.
- Cooling: Once the mold is filled, it’s cooled to solidify the plastic. This stage is crucial for maintaining the shape and structural integrity of the component.
- Quality Control: Finally, each molded part undergoes rigorous quality control inspections to ensure it meets all specifications and standards.
Applications of Precision Plastic Molding in Various Industries
Precision plastic molding finds applications across a wide range of industries due to its versatility and reliability. Here are some notable sectors where this technology shines:
1. Automotive Industry
In the automotive sector, precision molded components are essential for creating reliable parts such as dashboards, interior trim pieces, and exterior covers. The accuracy of these components contributes significantly to vehicle performance and safety.
2. Medical Devices
The medical industry heavily relies on precision plastic molding to manufacture critical components for devices like syringes, surgical instruments, and diagnostic equipment. The stringent quality standards in this sector make precision molding an ideal choice for ensuring patient safety and product reliability.
3. Electronics
With the ever-evolving electronics market, precision molded parts are crucial for creating housings, connectors, and various internal components. These parts require high precision to ensure optimal performance and fit into compact spaces.
4. Consumer Goods
From packaging to household items, precision plastic molding enables manufacturers to produce high-quality consumer goods that appeal to the masses. Products designed with this technology often feature enhanced aesthetic properties and functionality.
Benefits of Implementing Precision Plastic Molding
Adopting precision plastic molding techniques comes with numerous benefits that can significantly impact business operations:
- Streamlined Production: The precision of this molding technique allows for faster production cycles, reducing lead times and improving overall efficiency.
- Increased Flexibility: Manufacturers can easily adjust designs and specifications, which enables them to respond quickly to changing market demands.
- Enhanced Design Freedom: Designers can create complex shapes and structures that would be difficult to achieve through traditional manufacturing methods.
Challenges and Solutions in Precision Plastic Molding
Despite its many advantages, precision plastic molding is not without challenges. Common issues include:
1. Material Selection
Choosing the right material is critical. Manufacturers must consider factors such as thermal stability, strength, and compatibility with the molding process. Collaboration with material specialists can aid in selecting the most suitable options.
2. Tooling Costs
The initial investment in high-quality molds can be significant. However, the long-term savings from reduced waste and production efficiency can justify the upfront costs. Additionally, advanced technologies such as 3D printing can help lower these costs over time.
3. Precision Control
Maintaining consistent precision throughout the production process can be challenging. Implementation of robotic automation and advanced monitoring systems can enhance precision control and reduce human error.
Choosing the Right Manufacturer for Precision Plastic Molding
When selecting a manufacturer for precision plastic molding, it's essential to consider the following criteria:
- Experience: A manufacturer with a proven track record in precision molding will likely have the necessary expertise to meet your needs.
- Technology: Advanced machinery and technologies can enhance accuracy and efficiency in the molding process.
- Quality Assurance: Look for manufacturers that have strict quality control measures in place to ensure the highest standards are met.
- Customer Support: Reliable communication and support are crucial for addressing any concerns that may arise during production.
Future Trends in Precision Plastic Molding
The future of precision plastic molding is poised for exciting developments. Some trends to anticipate include:
1. Sustainable Practices
As environmental concerns rise, manufacturers are increasingly focusing on sustainable practices. This includes the use of recycled materials and energy-efficient processes to minimize the carbon footprint of production.
2. Automation and Robotics
The integration of automation and robotics in molding processes is set to increase production efficiency and precision, making it easier to meet the demands of the modern market.
3. Advanced Materials
New materials, including bio-based plastics and composites, are emerging, offering enhanced performance properties and sustainability features that cater to evolving consumer preferences.
Conclusion
Precision plastic molding represents a pivotal innovation in manufacturing, offering businesses the ability to produce high-quality and precise components that meet diverse industry demands. Embracing this technology not only enhances product performance but can also yield significant cost savings and efficiency improvements.
As industries continue to evolve, staying informed about advancements in precision plastic molding will provide businesses with a competitive edge. By selecting the right manufacturers and adopting best practices, organizations can harness the full potential of this transformative process.
For more information on precision plastic molding and its applications, visit deepmould.net.