Understanding Plastic Mold Injection: A Comprehensive Guide
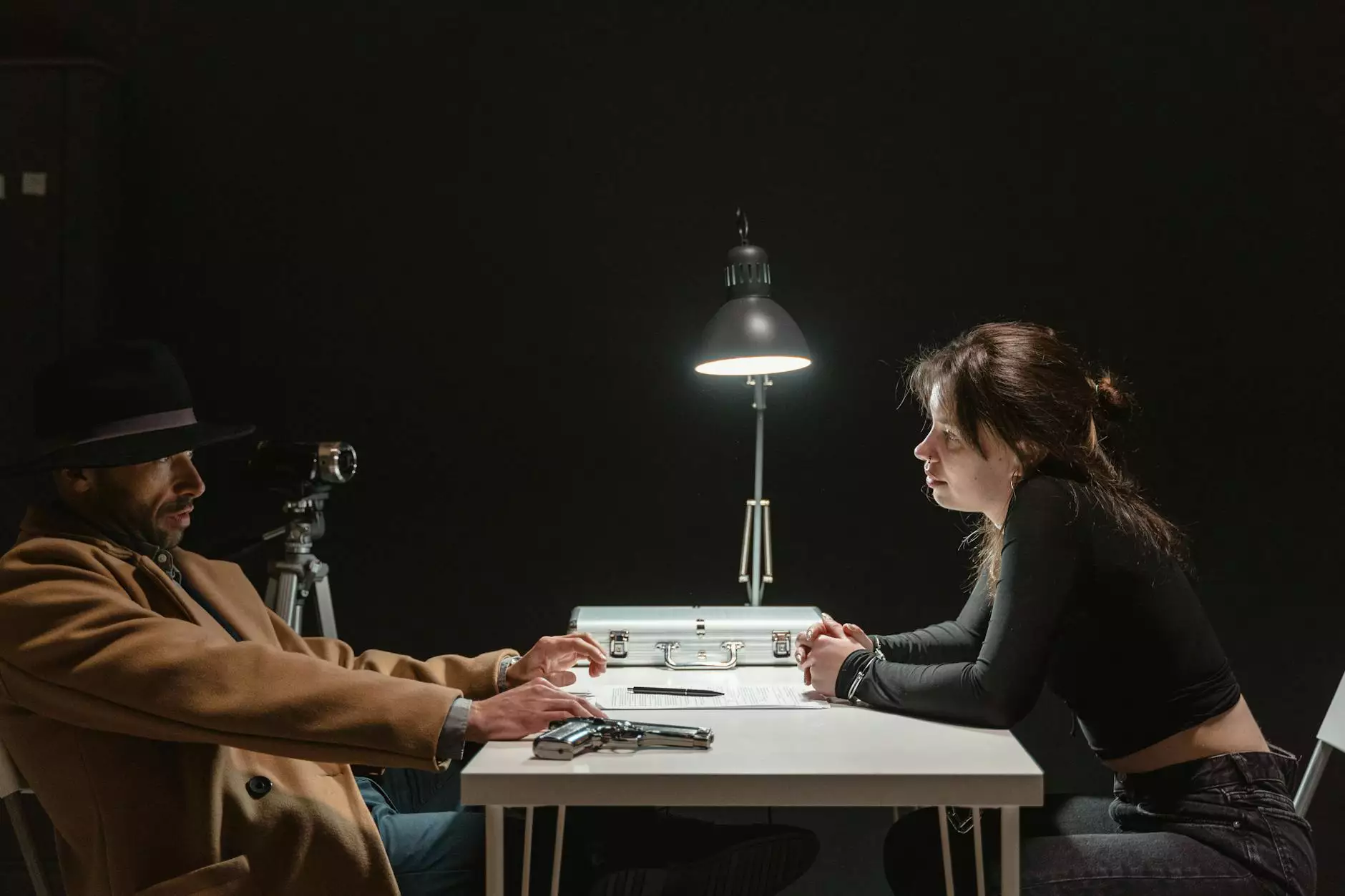
Plastic mold injection is a revolutionary manufacturing process that plays a pivotal role in various industries, particularly in the field of metal fabrication. This article delves into the intricacies of plastic mold injection, exploring its significance, methodology, advantages, and its impact on modern manufacturing. For businesses aspiring to enhance their production capabilities, particularly those listed under deepmould.net, understanding this technology is crucial.
The Basics of Plastic Mold Injection
Plastic mold injection is a process used to create plastic parts by injecting molten plastic into a mold. This technique is invaluable in producing complex shapes and high-precision components. The procedure can be broken down into several key stages:
- Material Selection: The type of plastic used can drastically affect the property of the molded part. Common materials include thermoplastics such as polypropylene, polystyrene, polyethylene, and nylon.
- Heating and Injection: The plastic is heated to its melting point, after which it is injected into the mold cavity under high pressure.
- Cooling: Once injected, the plastic cools and solidifies into the desired shape.
- Mold Release: The completed part is ejected from the mold, ready for finishing and assembly.
The Advantages of Plastic Mold Injection
The plastic mold injection process has numerous benefits that make it a preferred choice in manufacturing:
- High Efficiency: Once the mold is made, multiple parts can be produced quickly, significantly reducing production time and increasing output.
- Cost-Effectiveness: While mold creation can be expensive, the low cost per part made in high volumes offsets this initial investment.
- Complex Geometries: The process can produce intricate shapes and designs that may be impossible to achieve through other manufacturing methods.
- Material Flexibility: A wide range of plastic materials can be utilized, tailored to specific applications for mechanical strength and durability.
- Reduced Waste: The process is efficient in its use of materials, minimizing excess waste typically found in other manufacturing processes.
Applications of Plastic Mold Injection in Metal Fabrication
Plastic mold injection is not limited to just plastic products; it has a significant influence in the metal fabrication sector. Here’s how:
1. Functional Prototypes
Companies can rapidly produce functional prototypes of new designs using plastic mold injection. This allows for testing and evaluation of parts functionality before mass production, saving time and resources.
2. Composite Manufacturing
Integration of plastic components with metal parts is common. Plastic mold injection allows for precise and reliable manufacturing of plastic housings for metal components, enhancing overall product performance.
3. Assembly Components
Many assembly processes require a combination of both metal and plastic as components. Using plastic mold injection, businesses can create accurate and compatible plastic parts that integrate well with various metal elements.
Insights into the Plastic Mold Injection Process
Mold Design and Construction
The heart of the plastic mold injection process lies in the mold itself. Designing a mold that efficiently delivers molten plastic while ensuring accurate replication of the intended part is a complex yet critical task. Important aspects include:
- Material Selection: Molds are commonly made from steel or aluminum. Steel molds offer durability, while aluminum molds are faster to produce but less durable.
- Cooling Systems: Effective cooling channels are integrated into the mold design to expedite the cooling process, thus reducing production cycle times.
- Ventilation: Proper venting in molds prevents air traps and ensures the smooth flow of molten plastic.
Mold Maintenance
Like any machinery, molds require regular maintenance to ensure long-term functionality. Factors influencing mold longevity include:
- Cleaning: Regular cleaning avoids material build-up that can affect the quality of parts.
- Inspection: Routine checks for wear and tear can prevent defects in produced parts.
- Repairs: Timely repairs can extend mold life and minimize costly downtime.
Future Trends in Plastic Mold Injection
The landscape of plastic mold injection is evolving. With advancements in technology, several trends are shaping the future:
1. Automation and Robotics
The integration of robotics and automation is becoming more prevalent in manufacturing. Automated systems enhance production speed and accuracy, reducing human error and improving workers' safety.
2. 3D Printing Integration
3D printing technology is increasingly being used to create mold parts, allowing for faster prototype testing and reduced costs in initial mold production.
3. Eco-Friendly Materials
Sustainability is a major focus. The rise of biodegradable and recycled plastic materials is impacting the choice of materials used in plastic mold injection.
Conclusion
In conclusion, plastic mold injection is a critical process that drives efficiency and innovation in both the plastic and metal fabrication industries. Its ability to produce complex shapes at high volumes offers unparalleled advantages, making it an essential factor for businesses seeking to remain competitive in today's market. With ongoing advancements in technology and materials, the future of plastic mold injection looks promising, ready to adapt to the changing demands of various industries. Adopting this technology can lead to significant improvements in production quality, cost-effectiveness, and overall business growth.
Get Started with Plastic Mold Injection Today!
If your business is exploring ways to innovate and elevate production processes, consider incorporating plastic mold injection into your operations. For support, insights, and custom solutions, visit deepmould.net today!