Exploring the Role of Die Casting Components Manufacturers in Modern Industry
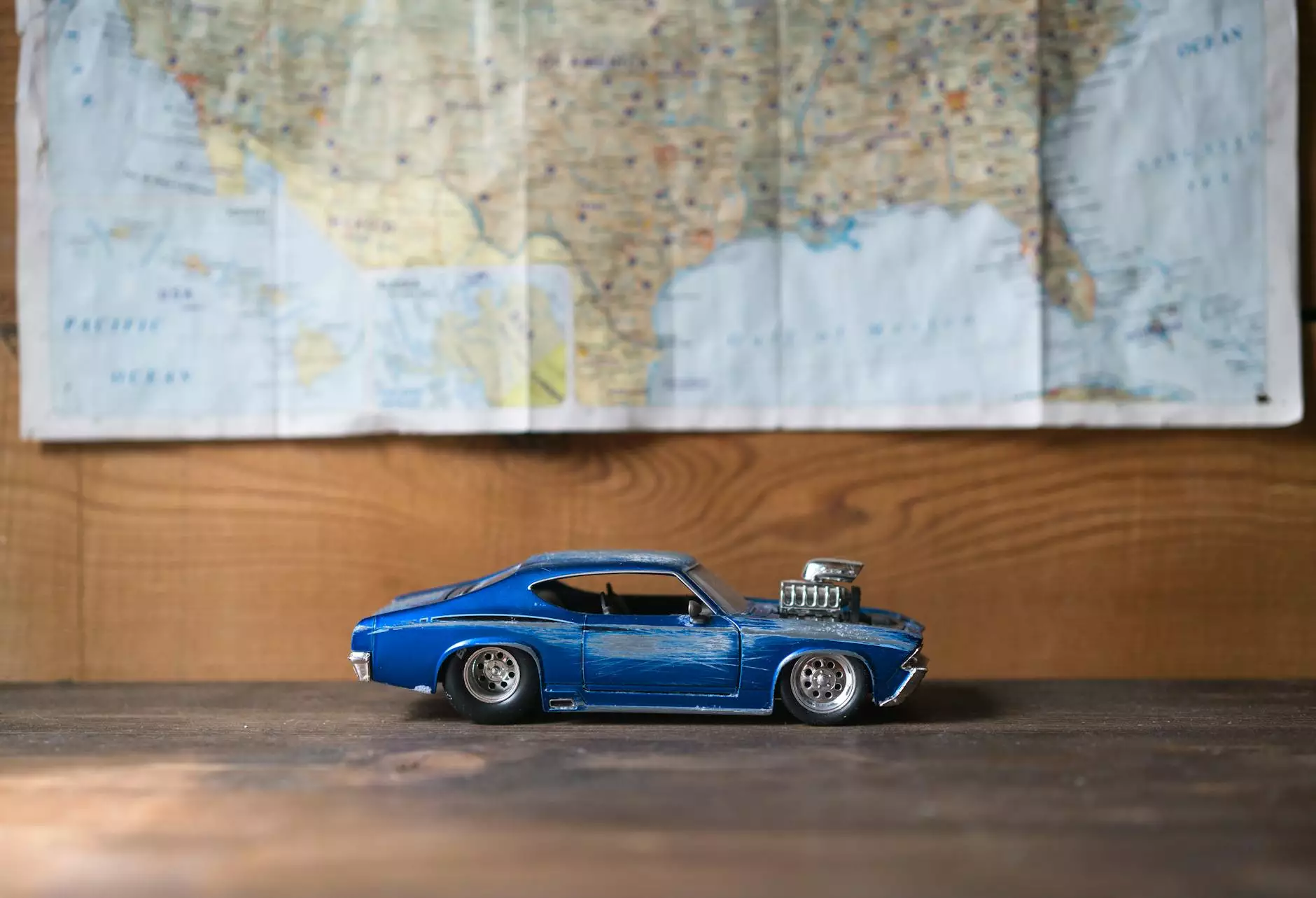
The manufacturing world is constantly evolving, driven by technological advancements and the demand for high-quality products across various industries. Among the key contributors to this evolution are die casting components manufacturers. These specialists play an integral role in producing components that cater to the needs of diverse applications, from automotive to electronics. In this article, we delve into the significance, processes, advantages, and future of die casting in manufacturing.
What is Die Casting?
Die casting is a metal casting process characterized by forcing molten metal under high pressure into a mold cavity. The molds are typically made of alloy steel, allowing for the production of complex shapes with high precision. This method is renowned for its ability to produce parts that require minimal secondary machining, thereby reducing production time and costs.
Advantages of Die Casting
- High Precision: Die casting enables manufacturers to achieve intricate designs with tight tolerances, ensuring consistency and uniformity across production runs.
- Efficiency: The process allows for high-volume production, which is essential for meeting the demands of industries that require rapid manufacturing solutions.
- Material Versatility: A variety of metals, including aluminum, zinc, magnesium, and copper alloys, can be utilized in die casting, making it suitable for numerous applications.
- Cost-Effectiveness: Although initial setup costs may be high, the long-term savings from reduced waste and enhanced production efficiency make die casting a cost-effective solution.
Key Types of Die Casting Processes
Understanding the different types of die casting processes is crucial for selecting the appropriate method for a specific application. Here are the main types often utilized by die casting components manufacturers:
1. Hot Chamber Die Casting
This process involves using a heated chamber for melting the metal. Here, the molten metal is injected into the mold while it is still hot. This method is primarily used for metals with low melting points, such as zinc and lead. It is known for its fast cycle times and is commonly used in producing parts for the automotive and electronics industries.
2. Cold Chamber Die Casting
In this method, the molten metal is poured into a cold chamber before being injected into the mold. This approach allows for the use of higher melting point metals, like aluminum and copper. Although cycle times may be slower than hot chamber die casting, it excels in producing larger components with intricate details and robust physical properties.
3. Gravity Die Casting
Unlike the pressure methods, gravity die casting relies on gravity to fill the mold. Typically used for high-quality castings, this process is less intensive and can lead to better structural integrity in the finished parts. It’s often used in industries where performance is key, such as aerospace and defense.
Industries Benefiting from Die Casting
Die casting components manufacturers serve a multitude of industries. Here are some notable sectors that benefit from this manufacturing process:
1. Automotive Industry
The automotive sector relies heavily on die casting to produce engine components, transmission housings, and other critical parts. The precision and durability offered by die casting ensure that automotive manufacturers can maintain high standards for safety and performance.
2. Electronics Industry
With the increasing demand for compact and efficient electronic devices, die casting provides solutions for creating lightweight yet strong enclosures for electronic components. Aluminum die casting, in particular, is favored for its thermal conductivity and aesthetic finish.
3. Aerospace Industry
The aerospace industry demands the highest quality components, as safety and performance are paramount. Die casting leads to the production of lightweight yet strong parts that can withstand extreme temperatures and conditions, making it indispensable in this field.
4. Consumer Products
From household appliances to furniture fittings, die casting offers an excellent solution for producing reliable and aesthetically pleasing consumer products. The versatility of materials and designs ensures that manufacturers can meet the diverse needs of consumers.
The Role of Quality Control in Die Casting
As with any manufacturing process, quality control is vital in ensuring that die cast products meet the required standards. Die casting components manufacturers employ various quality assurance techniques, including:
- Visual Inspections: Regular checks for surface defects such as cracks or voids.
- Dimensional Checks: Ensuring parts meet specified tolerances through precision measuring tools.
- Mechanical Testing: Conducting tensile tests to evaluate the physical properties of the cast parts.
Future Trends in Die Casting
The die casting industry is poised for evolution in the coming years, with several trends shaping its future:
1. Automation and Industry 4.0
As technology continues to advance, the integration of automation and smart technologies into die casting processes is on the rise. Die casting components manufacturers are adopting robotics and AI to enhance efficiency, improve quality, and reduce labor costs. These innovations make production processes more agile and responsive to market demands.
2. Sustainable Manufacturing Practices
Environmental concerns are pushing die casting manufacturers towards sustainable practices. This includes utilizing recyclable materials, reducing energy consumption, and minimizing waste generation.
3. Advanced Materials
The quest for enhanced performance is directing research toward new alloy compositions and material treatments. The development of innovative materials promises to unlock new applications and improve the properties of die cast components.
Choosing a Reliable Die Casting Manufacturer
When selecting a die casting components manufacturer, consider the following factors to ensure quality and reliability:
- Experience and Expertise: Look for manufacturers with extensive experience in the industry and a proven track record of delivering high-quality parts.
- Technological Capability: Ensure that the manufacturer utilizes advanced die casting techniques and equipment to produce precision components.
- Quality Assurance Processes: Assess their commitment to quality through robust inspection and testing methodologies.
- Customer Support: Reliable communication and support are essential for a successful partnership. Choose manufacturers who prioritize customer relations.
Conclusion
In summary, die casting components manufacturers play a pivotal role in modern manufacturing across various industries. By embracing advanced technologies and sustainable practices, these manufacturers continue to innovate and meet the increasingly complex demands of the market. Whether you are involved in the automotive, aerospace, electronics, or consumer products sector, understanding the value and advantages of die casting can help you make informed decisions in your supply chain and product development strategies. As the industry evolves, staying informed about trends and advancements will equip you to capitalize on the benefits of this vital manufacturing process.